ESG 2023 – Sustainability Statement
Download Enapter ESG 2023 Sustainability Statement
Foreword
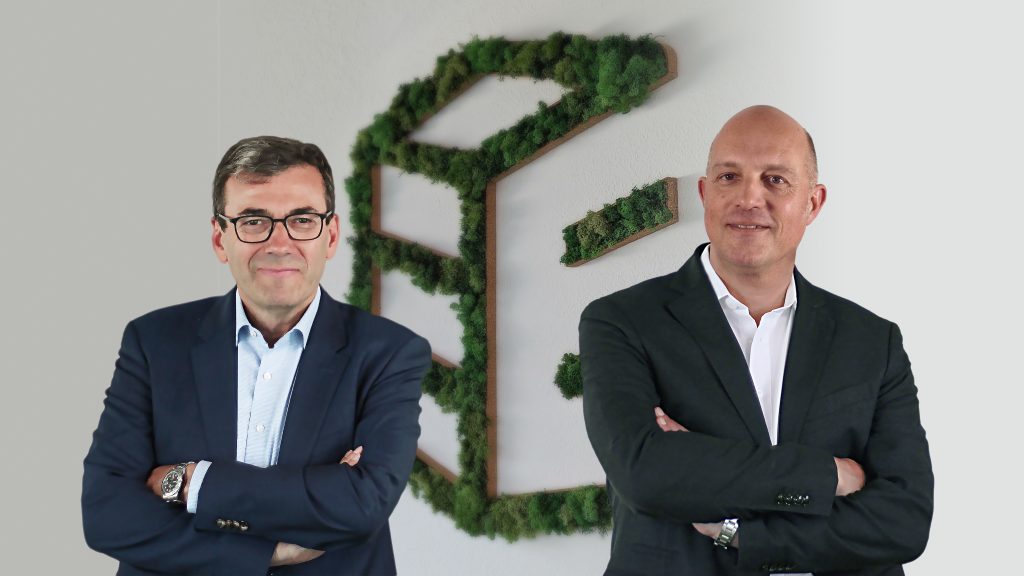
Enapter is the commercial leader in AEM electrolysis, a disruptive technology that we believe has the potential to make green hydrogen affordable and accessible to all – and end the use of fossil fuels. We know that our patented Anion Exchange Membrane (AEM) Electrolysers are what will get us there. Our modular electrolysers can be deployed to create green hydrogen production systems for any application, from the kilowatt scale to multi-megawatt solutions.
We try to minimize our impact on the environment at every step of the way, an ambition we are pursuing via the project “Life Cycle Impact Zero”. Both our production sites in Saerbeck and Pisa run on 100% renewable energy. Furthermore, we are reducing our CO2 emissions (Scope 1 and 2) by more than 90%, way ahead of our competition and much faster than what is achievable even by China and Taiwan. We are also embracing circularity principles and have already committed ourselves to taking back our electrolysers at the end of their lifetime.
The purpose of this very first Sustainability Statement is to give our partners and stakeholders an overview of where we stand today, what we have learnt about our environmental footprint and which ambitious plans we have for the future.
As a German listed SME, Enapter is not yet required to report in line with the newly adopted European Sustainability Reporting Standards (ESRS). We have published this report in line with ESRS regulation, both to demonstrate our ambition to be best-in-class in sustainability reporting and to be ready for the future. While this new format might feel unfamiliar to a new reader, this is what ESG and sustainability reporting will look like going forward. We decided to be ahead of the curve and adapt to the new regulations now. To our knowledge, we are the first electrolyser manufacturer structuring our sustainability report fully in line with ESRS.
We hope that this report provides you with valuable insights into our work and demonstrates our endeavour to do business in a way that maximises deployment of green hydrogen solutions while minimising harm to the planet. We would love to hear your feedback! Please do reach out to us anytime with concerns, comments or new ideas. We look forward to hearing from you.
Enjoy reading!
Jürgen Laakmann, CEO Enapter
and
Gerrit Kaufhold, CFO Enapter
General Information
ESRS 2 General Disclosures
BP-1 – Basis for preparation
This sustainability statement was prepared on a consolidated basis for Enapter AG and its subsidiaries Enapter S.R.L., Enapter GmbH, Enapter Immobilien GmbH , and Enapter LLC for the year 2023, in line with the Consolidated Financial Statements as of December 31, 2023. Enapter AG acts as an investment company that provides management and functional services to the subsidiaries it controls. It is also responsible for the financing of the group. This statement entails Enapter’s Corporate Carbon Footprint for the years 2022 and 2023, calculated in line with the Greenhouse Gas Protocol (GHG Protocol), i.e. including Enapter AG and its subsidiaries. In the future, it will include other companies over which Enapter AG has operational control, to comply with ESRS E1-6, paragraph 50.
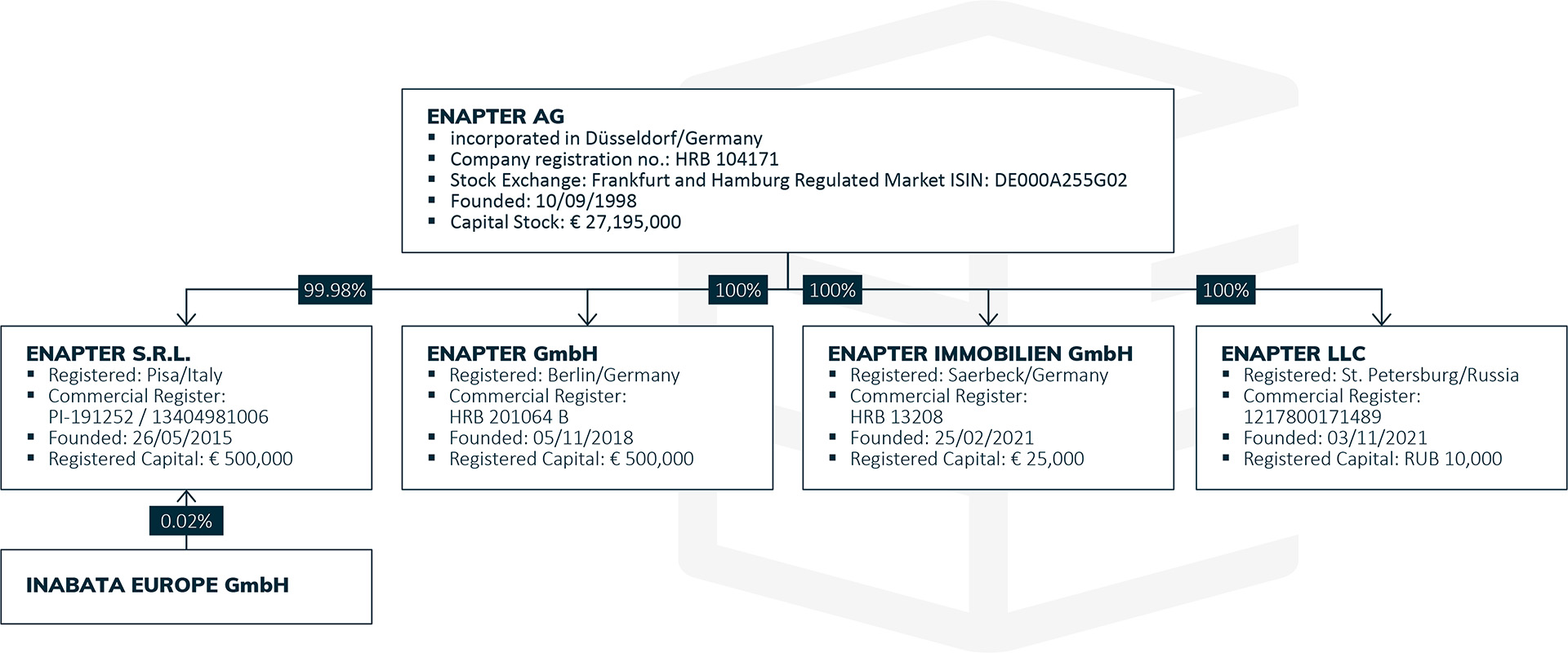
Enapter’s upstream and downstream value chains have been included in this statement to the best of our capacities. We aim to gradually extend the scope of information included in the future. Value chain information was taken into account in the materiality analysis of impacts, risks and opportunities, in Enapter’s Environmental Policy and in the Corporate Carbon Footprint’s Scope 3 calculations.
We have used the option provided by ESRS 1 section 7.7 to provide only aggregated information about our electrolyser’s stack in this statement, for example in the Corporate Carbon Footprint (Section E1-6) and in resource inflows and outflows (Sections E5-4 and E5-5), as it corresponds to intellectual property, know-how or the results of innovation.
SBM- 1 – Strategy, business model and value chain
Enapter is a company making a substantial contribution to decarbonising the global economy. We consider the cost-effective production and use of green hydrogen an indispensable part of our mission. Our company’s business is the production of AEM electrolysers, which we have patented after almost two decades of research. We are the commercial leader in AEM technology and work towards continuously expanding this lead, which means maintaining technology and cost leadership within the AEM electrolysis segment. Enapter is a pioneer in sustainable industrial production: Our two sites in Pisa and Saerbeck are powered by 100% renewable electricity.
Enapter focuses on the customer segments mobility, industrial hydrogen applications and electricity storage. Over half of our clients use our electrolysers to bring power to their communities, stabilise the electricity grid or make their businesses or homes energy independent. Industrial innovators use green hydrogen to pioneer new industrial applications: Power-to-X, green ammonia and bio-methane are just a few of the applications our industrial customers unlock with the help of our electrolysers. We are furthermore pushing the agenda with our clients from the industrial heat segment, aiming to decarbonise their heat requirements through blending hydrogen from our electrolysers with natural gas. Our electrolysers provide a compact solution for any refuelling need. Mobility clients use them for on-site hydrogen production for their mobility applications: Trucks, buses, cars and corporate fleets.
Thanks to our modular product approach, our AEM stacks can be used as minimum modular units in systems of different sizes. This means that we build different products on a single stack design. We use our stacks both for single-core electrolysers, which cover projects up to approx. 120 kW, and for multi-core electrolysers (AEM Flex and AEM Nexus), which cover the megawatt range.
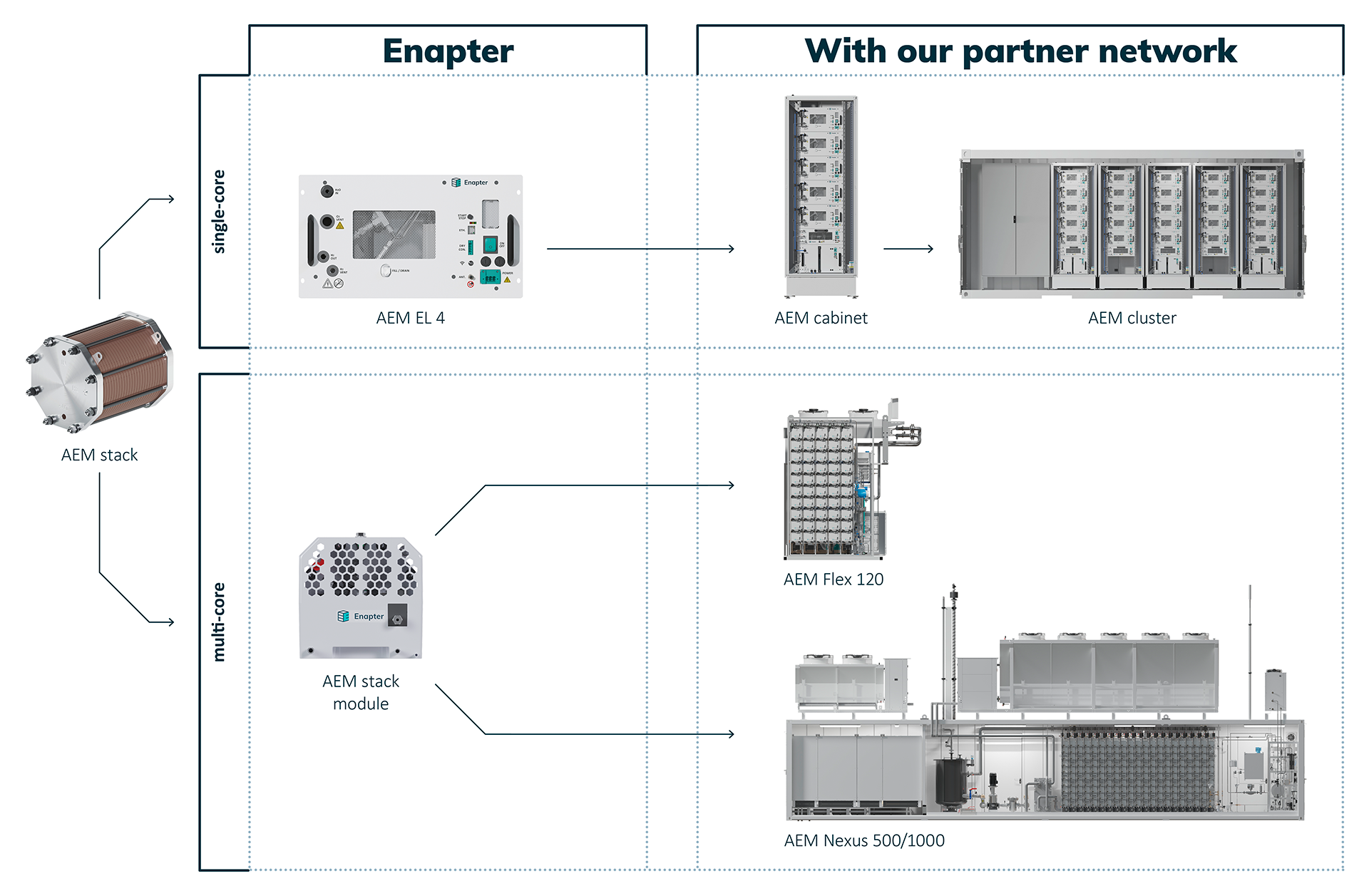
Our AEM electrolysers are flexible building blocks for energy projects with green hydrogen: one electrolysis module, several modules stacked or scaled to megawatts.
We are pursuing the ambition to minimise any negative impact on people and the planet with the project “Life Cycle Impact Zero”. In the context of this project, we have been calculating our Corporate Carbon Footprint (CCF) on a yearly basis since 2022 with the support of independent researchers from Fraunhofer UMSICHT. The latter have also undertaken a lifecycle analysis of all our products, with the objective to further optimise our respective environmental impact. We are constantly striving to improve the quality of our products, i.e. increasing their total lifespan and decreasing our need for natural resources while increasing the amount of green hydrogen produced by our electrolysers. We also work on design changes, which will improve reusability, repairability and recyclability, and will significantly reduce waste. Last but not least, we have the ambitious goal to circularise our production as much as possible, by taking back all our products at their end of life and maximising the amount of components and materials we re-use, repair and recycle.
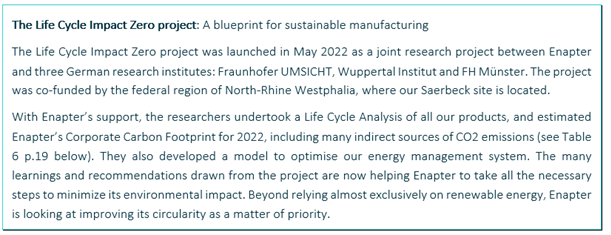
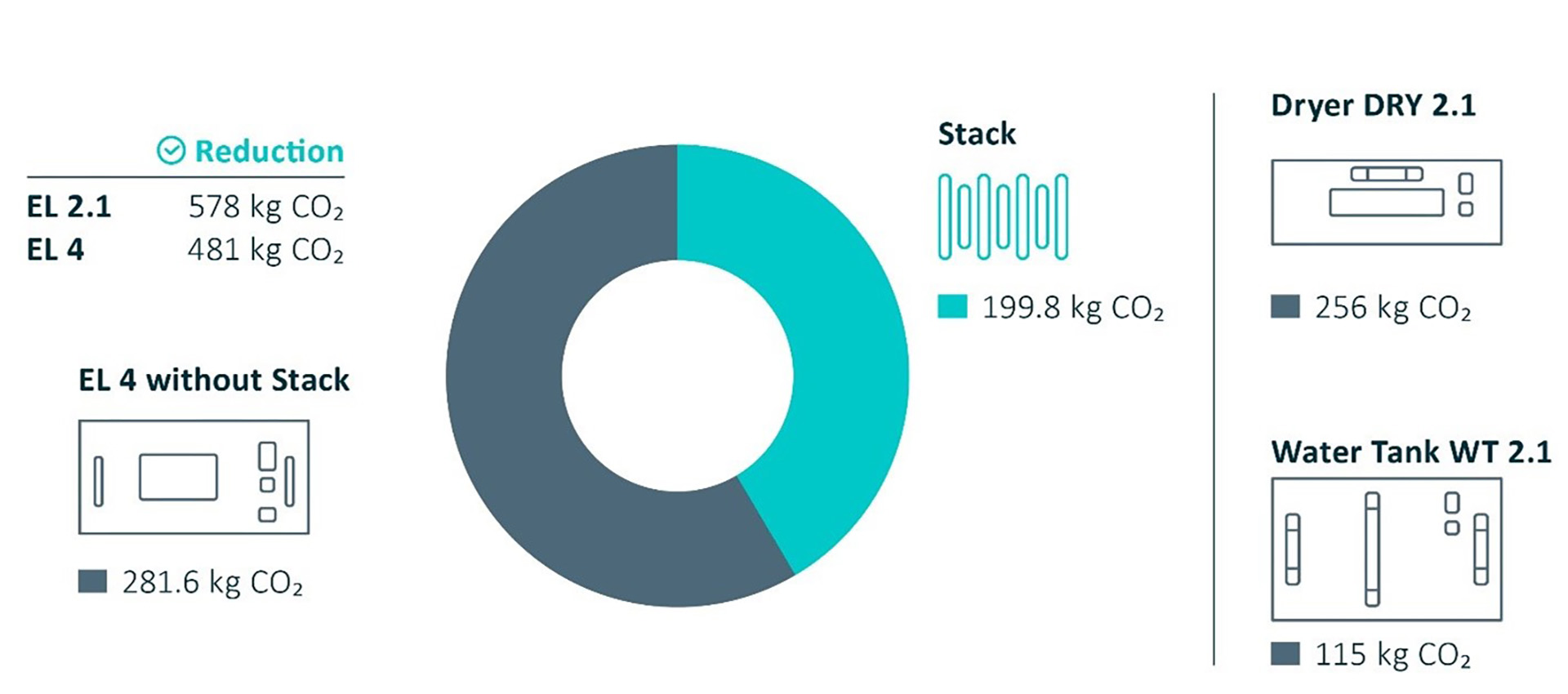
As a product manufacturer, Enapter purchases numerous mechanical, electronical and chemical product components and raw materials to transform and assemble them into electrolysers. Due to the complexity of its products, Enapter has both a very broad and very deep upstream value chain, entailing several hundreds of individual Tier-1 suppliers, from SMEs to corporates, and several thousands of Tier-2, Tier-3 suppliers and above. The vast majority of Enapter’s Tier-1 suppliers are located in Northern Italy (in particular, in and around Milan), as well as in Germany for the components of the AEM Nexus. Only a few suppliers are located, for example, in the US and in China. Given the current distribution of international trade, we assume (without being in a position to verify it for every single company) that most of our Tier-2 suppliers, which are manufacturers of metallic and plastic raw materials and electronic components, are located in Asia, and in particular in China and Taiwan. Tier 3+ suppliers, which are mostly suppliers of raw materials, are assumed to be located in various raw material extracting countries around the world.
Our Tier-1 suppliers are selected based on a thorough due diligence process, in which we review the quality, availability and price of their products as well as their environmental and social performance. Based on the long-term relationships we have built with them, we have no reason to believe that they face any material environmental, social or governance sustainability issues. Given the sheer number of our Tier 2+ suppliers, we cannot evaluate potential sustainability issues with all of them, but we will increasingly raise material sustainability topics with our Tier-1 suppliers and request them to evaluate these with their suppliers.
In 2022-2023, Enapter conducted an exhaustive raw material criticality analysis in the framework of the sustainability research project “Life Cycle Impact Zero”, with the support of the Wuppertal Institute. The analysis showed that for the vast majority of product components and materials, Enapter is either not exposed to a criticality risk or has the right procurement and production strategies in place to mitigate such risks. Such strategies include long-term purchasing agreements with suppliers, securing of safety stocks and listing alternative suppliers for critical components, among others. An additional analysis was conducted internally for our electrolyser’s stack and identified some potential for improvement, which will be addressed by our R&D department.
Enapter’s downstream value chain is composed mainly of a globally active network of integration partners, i.e. engineering companies that integrate our electrolysers into turnkey hydrogen production systems for their own customers. In 2023, Enapter granted an exclusive distribution license to Clean H2 in the US and entered into a Joint Venture with Wolong Group in China in the beginning of 2024. Our partner network and customer base are diversifying and growing strongly from year to year. In line with our Code of Conduct, we expect from all our business partners to adhere to the same standards as we do. Enapter has no indications that these partners face any material environmental, social or governance sustainability issues.
Another small group of downstream value chain partners are recyclers and waste management partners. As an SME, Enapter produces relatively little waste. While our resource efficiency will increase further in the future, absolute amounts of waste will increase in correlation with our company’s growth. Hence, recyclers and waste management companies will become a more important group of partners in the future, especially as Enapter strives to recover all products at the end of their lifecycle for disassembly, re-use and recycling. In this area, it is of utmost importance that Enapter ensures that its recycling partners handle its waste in full compliance with applicable laws and regulations. To mitigate this potentially growing pollution risk, Enapter plans to deepen and diversify its relationships with recyclers and waste managers in the future.
SBM-2 – Interests and views of stakeholders
Enapter’s main stakeholders are summarized in the table below:
Stakeholder category | Stakeholder’s interest in Enapter | Enapter’s current interaction with stakeholder | Stakeholder’s contact at Enapter | Enapter’s strategy to address the interests of stakeholders |
Investors | Increasing, foreseeable value creation Expansion of ESG portfolio with companies that are in growth / post-venture stage | Regular one-on-one meetings with existing and potential (strategic) investors Enapter representation at leading national and international investor conferences and forums Hosting annual investor “Info Day” | C-Level VPs Investor Relationship Team | Tailor existing and future reporting efforts to specific investor groups Further increase transparency on strategic outlook |
Suppliers | Increasing, foreseeable purchase Long-term supply partnerships | Constant alignment via regular calls Supplier agreements Site visits and audits Annual supplier meetings | VPs Supply Chain Management Team | Improve Enapter’s understanding of suppliers and their needs via supplier questionnaire / online portal |
Own workforce | Good working conditions Career advancement opportunities Meaningful job | Annual employee performance reviews Regular all-hands and leadership meetings | HR Team VPs Team Leads | Flat company hierarchy Stock options programme Ongoing improvement in setting up effective internal communication channels |
Customers | Timely supply of high-quality electrolysers Simple integration into their hydrogen production systems Support and maintenance | Constant alignment via regular calls Site visits Service agreements Promotion of use cases via marketing channels and joint campaigns | Business Development Sales and Service Teams | Partner trainings Constant optimisation of partnership programme Joint marketing campaigns |
Government | Socio-economic value creation (in particular employment) Promote national pioneers in green economy | Regular exchange in relevant committees and forums Consultations on regulatory topics concerning electrolysers | C-Level VPs | Promote Enapter’s role as an international expert in AEM technology |
Civil Society (Research institutes, business associations, like-minded partners, public) | Industry or scientific insights Socio-economic impact | Transparent communication via social media Joint R&D projects Information exchange via calls, reports or participation in conferences | R&D Team Marketing Team VPs | Promote Enapter’s role as an international expert in AEM technology |
Impact, risk and opportunity management
DR IRO 1: Description of the processes to identify and assess material impacts, risks and opportunities
The materiality analysis of this sustainability statement is based on selective consultations with external stakeholders, employees, investors and reporting experts.
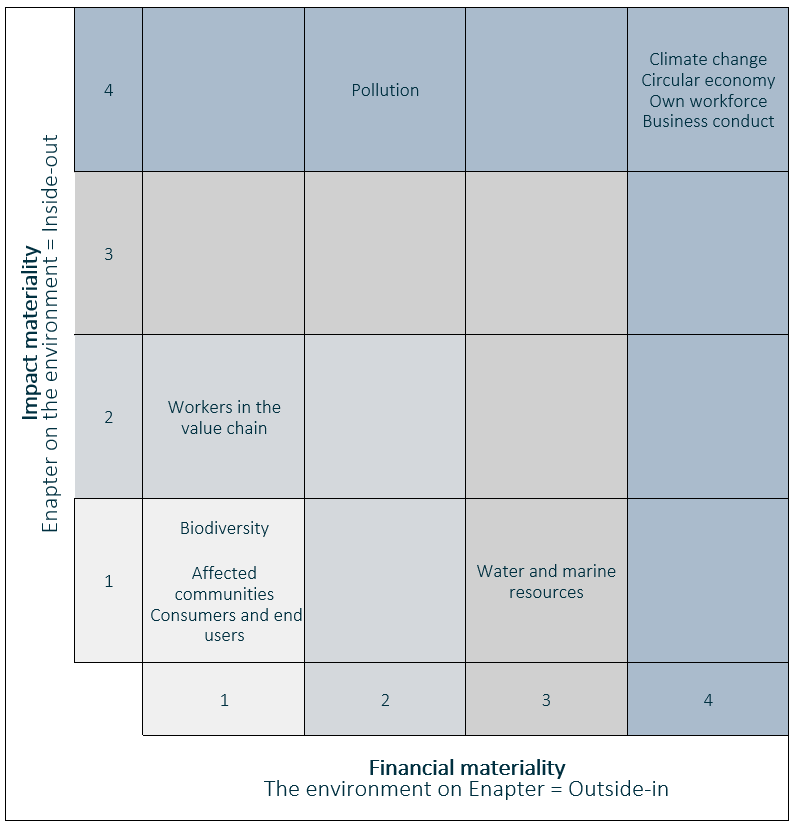
In line with ESRS 1 Chapter 3, all 10 main topics, 37 sub-topics and 73 sub-sub-topics (henceforth “topics”) were carefully reviewed and assessed both from a financial materiality perspective (impact of the outside world on Enapter) and from an impact materiality perspective (impact of Enapter on the outside world). The financial materiality of all topics was assessed against the risks and opportunities deriving from them for Enapter, as well as the likelihood of their occurrence and the magnitude of their (potential) financial effects. The impact materiality of all topics was assessed against their severity (in terms of scope, scale and irremediable character) and, for potential impacts, their likelihood. All topics were assessed from 1 (low materiality) to 4 (high materiality). Ultimately, a matrix was developed to reflect the position of all main topics on two axes (financial and impact materiality). All main topics placed on 4 at least on one of the two axes were considered material and are reported upon in this sustainability statement.
DR IRO 2: Disclosure requirements in ESRS covered by the undertaking’s sustainability statement
Disclosure Requirement | Disclosure | Reason for non-disclosure | Disclosure page |
ESRS 2 – GENERAL DISCLOSURES | Yes | — | 4 |
BP-1 – General basis for preparation of sustainability statements | Yes | — | 4 |
BP-2 – Disclosures in relation to specific circumstances | No | To be disclosed in a future statement | — |
GOV-1 – The role of the administrative, management and supervisory bodies | No | To be disclosed in a future statement | — |
GOV-2 – Information provided to and sustainability matters addressed by the undertaking’s administrative, management and supervisory bodies | No | To be disclosed in a future statement | — |
GOV-3 – Integration of sustainability-related performance in incentive schemes | No | To be disclosed in a future statement | — |
GOV-4 – Statement on due diligence | No | To be disclosed in a future statement | — |
GOV-5 – Risk management and internal controls over sustainability reporting | No | To be disclosed in a future statement | — |
SBM-1 – Strategy, business model and value chain | Yes | — | 5 |
SBM-2 – Interests and views of stakeholders | Yes | — | 8 |
SBM-3 – Material impacts, risks and opportunities and their interaction with strategy and business model | No | To be disclosed in a future statement | — |
IRO-1 – Description of the processes to identify and assess material impacts, risks and opportunities | Yes | — | 11 |
IRO-2 – Disclosure requirements in ESRS covered by the undertaking’s sustainability statement | Yes | — | 12 |
MDR-P – Policies adopted to manage material sustainability matters | Yes | — | 15 |
MDR-A – Actions and resources in relation to material sustainability matters | No | To be disclosed in a future statement | — |
MDR-T – Tracking effectiveness of policies and actions through targets | No | To be disclosed in a future statement | — |
ESRS E1 CLIMATE CHANGE | Yes | — | 15 |
E1-1 – Transition plan for climate change mitigation | Yes | — | 15 |
E1-2 – Policies related to climate change mitigation and adaptation | Yes | — | 16 |
E1-3 – Actions and resources in relation to climate change policies | No | To be disclosed in a future statement | — |
E1-4 – Targets related to climate change mitigation and adaptation | No | To be disclosed in a future statement | — |
E1-5 – Energy consumption and mix | Yes | — | 17 |
E1-6 – Gross Scopes 1, 2, 3 and Total GHG emissions | Yes | — | 18 |
E1-7 – GHG removals and GHG mitigation projects financed through carbon credits | Yes | — | 22 |
E1-8 – Internal carbon pricing | No | To be disclosed in a future statement | — |
E1-9 – Anticipated financial effects from material physical and transition risks and potential climate-related opportunities | No | To be disclosed in a future statement | — |
ESRS E2 POLLUTION | Yes | — | 23 |
E2-1 – Policies related to pollution | Yes | — | 23 |
E2-2 – Actions and resources related to pollution | Yes | — | 23 |
E2-3 – Targets related to pollution | No | To be disclosed in a future statement | — |
E2-4 – Pollution of air, water and soil | Yes | — | 23 |
E2-5 – Substances of concern and substances of very high concern | Yes | — | 24 |
E2-6 – Anticipated financial effects from material pollution-related risks and opportunities | No | To be disclosed in a future statement | — |
ESRS E3 WATER AND MARINE RESOURCES | No | Non-material | |
ESRS E4 BIODIVERSITY AND ECOSYSTEMS | No | Non-material | |
ESRS E5 RESOURCE USE AND CIRCULAR ECONOMY | Yes | — | 24 |
E5-1 – Policies related to resource use and circular economy | Yes | — | 24 |
E5-2 – Actions and resources related to resource use and circular economy | Yes | — | 24 |
E5-3 – Targets related to resource use and circular economy | Yes | — | 25 |
E5-4 – Resource inflows | Yes | — | 25 |
E5-5 – Resource outflows | Yes | — | 26 |
E5-6 – Anticipated financial effects from resource use and circular economy-related impacts, risks and opportunities | No | To be disclosed in a future statement | |
ESRS S1 OWN WORKFORCE | Yes | — | 28 |
ESRS 2 SBM-2 – Interests and views of stakeholder | Yes | — | 28 |
ESRS 2 SBM-3 – Material impacts, risks and opportunities and their interaction with strategy and business model | No | To be disclosed in a future statement | — |
S1-1 – Policies related to own workforce | Yes | — | 28 |
S1-2 – Processes for engaging with own workers and workers’ representatives about impacts | No | To be disclosed in a future statement | — |
S1-3 – Processes to remediate negative impacts and channels for own workers to raise concerns | No | To be disclosed in a future statement | — |
S1-4 – Taking action on material impacts on own workforce, and approaches to mitigating material risks and pursuing material opportunities related to own workforce, and effectiveness of those actions | No | To be disclosed in a future statement | — |
S1-5 – Targets related to managing material negative impacts, advancing positive impacts, and managing material risks and opportunities | No | To be disclosed in a future statement | |
S1-6 – Characteristics of the undertaking’s employees | Yes | — | 29 |
S1-7 – Characteristics of non-employees in the undertaking’s own workforce | Yes | — | 30 |
S1-8 – Collective bargaining coverage and social dialogue | Yes | — | 29 |
S1-9 – Diversity matrix | Yes | — | 30 |
S1-10 – Adequate wages | Yes | — | 30 |
S1-11 – Social protection | Yes | — | 30 |
S1-12– Persons with disabilities | Yes | — | 30 |
S1-13 – Training and skills development metrics | Yes | — | 30 |
S1-14 – Health and safety metrics | Yes | — | 31 |
S1-15 – Work-life balance metrics | Yes | — | 31 |
S1-16 – Remuneration metrics (pay gap and total remuneration) | Yes | — | 31 |
S1-17 – Incidents, complaints and severe human rights impacts | Yes | — | 31 |
ESRS S2 WORKERS IN THE VALUE CHAIN | No | Non-material | |
ESRS S3 AFFECTED COMMUNITIES | No | Non-material | |
ESRS S4 CONSUMERS AND END-USERS | No | Non-material | |
ESRS G1 BUSINESS CONDUCT | Yes | 31 | |
G1-1– Business conduct policies and corporate culture | Yes | — | 31 |
G1-2 – Management of relationships with suppliers | Yes | — | 32 |
G1-3 – Prevention and detection of corruption and bribery | Yes | — | 32 |
G1-4 – Incidents of corruption or bribery | Yes | — | 33 |
G1-5 – Political influence and lobbying activities | Yes | — | 33 |
G1-6 – Payment practices | Yes | — | 33 |
MDR-P – Policies adopted to manage material sustainability matters
Next to its Code of Conduct, Enapter has adopted a dedicated Environmental Policy and a Human Resources Policy to help prevent, mitigate and remedy actual and potential impacts, to address risks, and to pursue opportunities related to these two material sustainability matters.
Enapter’s Environmental Policy aims to commit Enapter’s employees, management and, potentially, stakeholders to environmental protection on all topics relevant in our business context: energy, purchasing, waste (including hazardous substances), water, biodiversity and transport. The policy also defines commitments related to transversal actions required to achieve its goals: calculation of our Corporate Carbon Footprint, implementation of lifecycle assessments, setup of an Environmental Management System, stakeholder engagement, reporting, circular economy, allocation of human and financial resources, and compliance. The policy applies to Enapter’s management and employees alike and touches upon topics applying globally to our entire upstream and downstream supply chain.
Enapter’s Human Resources Policy sets a framework for how our company deals with its own workforce and workers in our supply chain. It covers the following topics: working time, adequate wages, social dialogue, work-life balance, health and safety, gender equality and diversity, trainings and skills development, measures against violence and harassment, and prevention of child labour and forced labour. Enapter’s management, team leads, and HR and Purchase Teams are expressly responsible for the implementation of the HR policy. Enapter’s CEO Dr. Jürgen Laakmann has endorsed both policies and is accountable for their implementation
Environmental Information
ESRS E1 Climate change
DR E1-1: Transition plan for climate change mitigation
Enapter has developed a transition plan for climate change mitigation. This plan entails detailed projections of the company’s future development in all areas pertaining to its impact on climate change:
- Business growth
- Human resources
- Product development
- Greenhouse gas (GHG) emissions
- Recycling
- Carbon offsetting
- GHG emission avoidance
Each of these areas are further detailed into sub-areas: e.g. recycling contains the sub-areas metals, electronics, plastics and chemistry, while for GHG emissions, all Scope 1, 2 and 3 emissions are detailed under Disclosure Requirement E1-6, p.18.
Taking 2022 as a reference year, this transition plan provides estimates of how Enapter could develop until 2050, and how the different areas impact each other (e.g. how business growth or recycling impact GHG emissions, or how product development impacts GHG emission avoidance). Most importantly, this plan details internal actions which have been taken and should be taken to reduce Enapter’s negative impact on climate change and to increase its positive impact on climate change mitigation. It also clarifies which areas of Enapter’s sustainability depend on internal actions and which ones rely on external factors (e.g. the decarbonisation of mobility or of Enapter’s supply chain).
Enapter’s transition plan does not assume fully accurate projections that would be set in stone until 2050: It is instead a tool for reflection that helps the company analyse how its future development could affect climate change (both negatively and positively) and which actions could have consequences on the company’s overall sustainability in the long term.
Enapter has already taken two major climate change mitigation actions: Between winter 2022/2023 and winter 2023/2024, we switched to a combination of renewable electricity-based heating and pellet oven heating at our Saerbeck site. On November 1st, 2023, we then switched to an electricity provider based on 100% renewable energy at our Pisa site. Together, these actions decreased our Scope 1 and 2 emissions from combustion, electricity and heating by more than 90%. This not only far exceeds the recommended speed of the Sciences Based Target Initiative (SBTi) for bringing companies in line with the Paris Agreement1 ; it also brings Enapter very close to carbon neutrality for Scope 1 and 2 market-based emissions, only six years after its founding. More climate change mitigation actions will follow in the future, from production waste reduction to carbon offsetting, all the way to the circularisation of our production. Detailed targets and action plans will be developed on these crucial topics in the near future.
DR E1-2: Policies related to climate change mitigation and adaptation
Enapter exists to mitigate climate change by leveraging the power of AEM Electrolysers. We manufacture these machines that produce green hydrogen, with the mission to make this gas affordable and accessible to all. We are reducing hydrogen’s cost of production to make it competitive with fossil fuels in many applications and see that AEM has the potential to be the most inexpensive way to produce green hydrogen by 2030.2 Beyond contributing to the decarbonisation of diverse sectors with our AEM Electrolysers, we have set ourselves the ambitious goal of developing an entire production process that minimises negative impacts. In 2022, we started the “Life Cycle Impact Zero” project alongside independent researchers to examine our sustainability foundation and possible pathways for achieving this. Today, we already run our electrolyser manufacturing facilities on 100% renewable electricity. In the long term, we plan to follow the principles of circular economy to tend towards zero negative impact on people and the planet – acting as a role model for sustainable industrial production.
DR E1-5: Energy consumption and mix
Energy Consumption and Mix | 2023 | 2022 |
(6) Total fossil energy consumption (MWh) | 932.86 | 1142.19 |
Share of fossil sources in total energy consumption (%) | 39.4% | 61.8% |
(7) Consumption from nuclear sources (MWh) | 2.77 | 4.59 |
Share of consumption from nuclear sources in total energy consumption (%) | 0.1% | 0.2% |
(8) Fuel consumption from renewable sources, including biomass (also comprising industrial and municipal waste of biologic origin, biogas, renewable hydrogen, etc.) (MWh) | 3.15 | 25.95 |
(9) Consumption of purchased or acquired electricity, heat, steam, and cooling from renewable sources (MWh) | 1205.67 | 558.16 |
(10) The consumption of self-generated non-fuel renewable energy (MWh) | 222.76 | 116.25 |
(11) Total renewable energy consumption (MWh) (calculated as the sum of lines 8 to 10) | 1431.58 | 700.36 |
Share of renewable sources in total energy consumption (%) | 60.5% | 37.9% |
Total energy consumption (MWh) (calculated as the sum of lines 6, 7 and 11) | 2367.20 | 1847.13 |
Background information: Total delivered electrolyser capacity (MW) | 11.86 | 4.16 |
Furthermore, Enapter increased its solar PV production capacity at its Pisa plant from 64 kW to 144 kW in June 2022, and to a total of 305 kW in October 2022. Beyond the self-consumption disclosed above in Table 4, point 10, an additional 3,974 kWh were fed into the Italian electricity grid in 2022 and 157,545 kWh in 2023. This led to an estimated total of 50.8tCO2eq savings for Italian electricity grid consumers in the reporting period.3
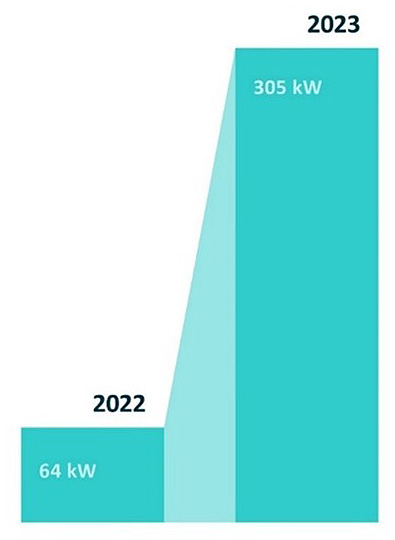
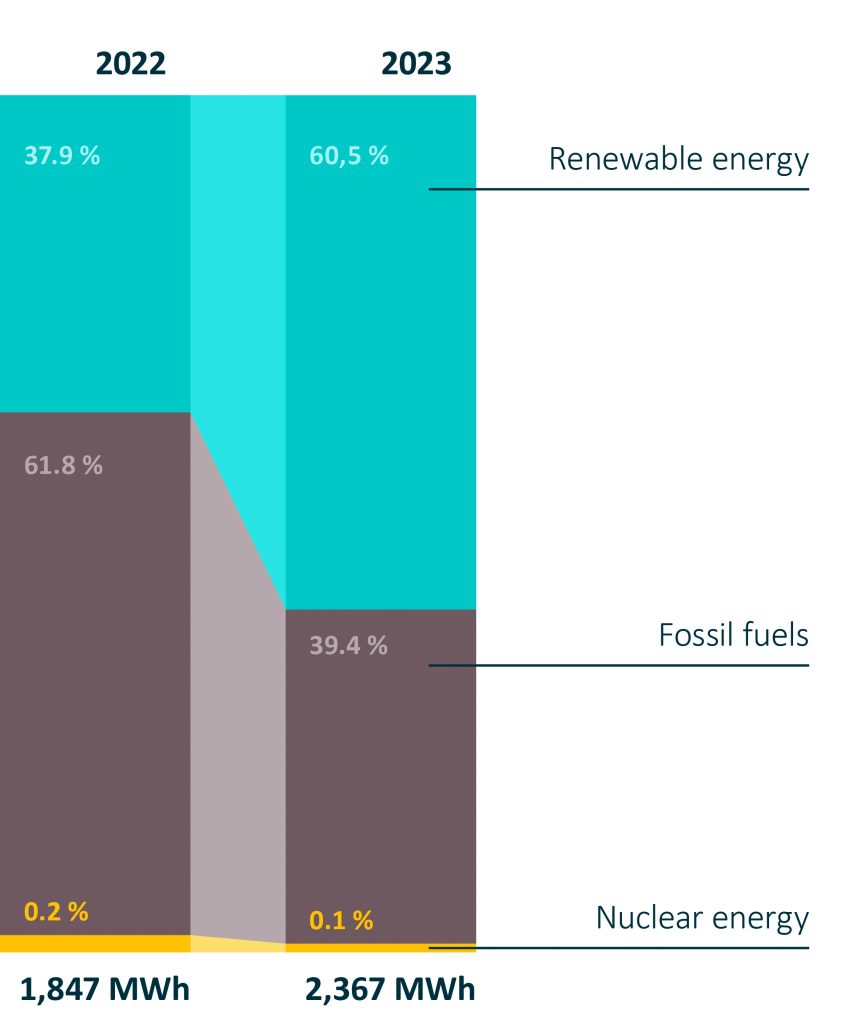
Figure 6 Energy mix
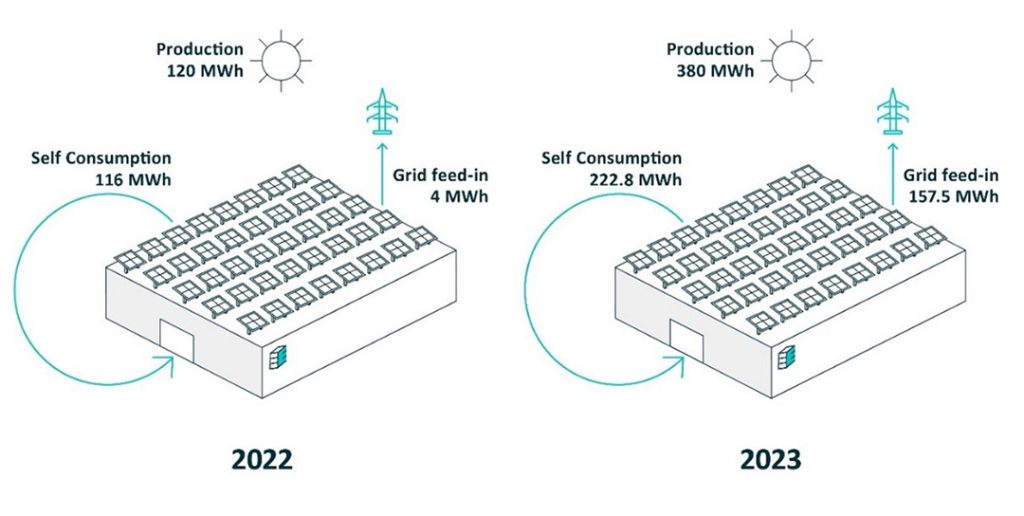
DR E1-6: Gross Scopes 1,2, 3 and Total GHG Emissions
Total Gross GHG Emissions (in tCO2eq) | 2023 | 2022 |
Total Scope 1 GHG Emissions | 212.8 | 101.8 |
Percentage of Scope 1 GHG emissions from regulated emission trading schemes | 0% | 0% |
Total Scope 2 GHG Emissions – location-based | 588.4 | 431.5 |
Total Scope 2 GHG Emissions – market-based | 308.0 | 429.8 |
Total Scope 3 GHG Emissions | 1790.6 | 1250.8 |
Total GHG emissions – location-based | 2591.8 | 1784.1 |
Total GHG emissions – market-based | 2311.3 | 1782.4 |
GHG Intensity | 2023 | 2022 | 2023/2022 |
-location-based – Scope 1 and 2 | 25.43 | 36.35 | 70% |
-market-based – Scope 1 and 2 | 16.53 | 36.24 | 46% |
-location-based – Scope 1, 2 and 3 | 82.28 | 121.61 | 68% |
-market-based – Scope 1, 2 and 3 | 73.37 | 121.49 | 60% |
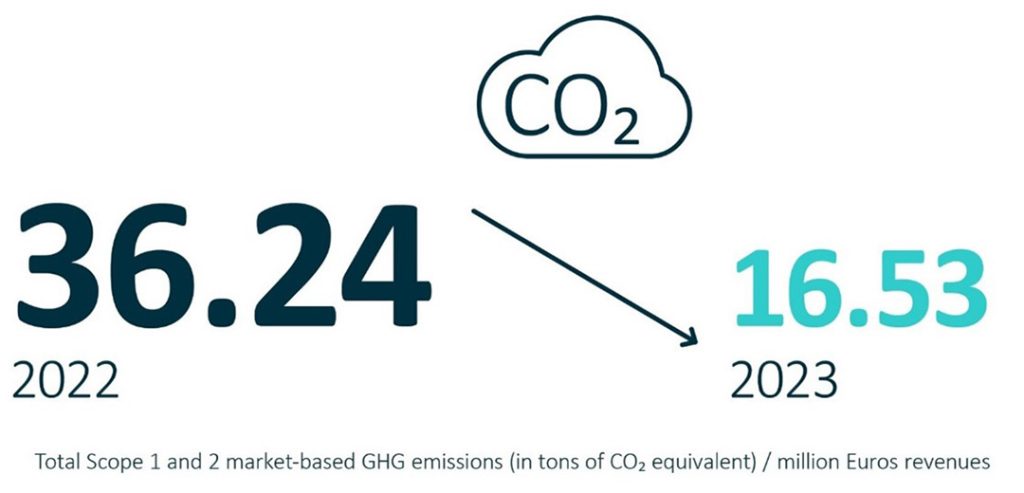
The GHG intensity is calculated as tons of CO2eq / € millions of net revenues. These revenue amounts stem from Enapter’s Financial Statements in 20224 and 20235.
Total Gross GHG Emissions (in tCO2eq) | 2023 | 2022 |
SCOPE 1 | ||
1.1. Stationary Combustion | 140.1 | 96.6 |
1.2. Mobile Combustion | 3.8 | 5.2 |
1.3. Process Emissions | 0 | 0 |
1.4. Cooling | 68.9 | 0 |
Total Scope 1 GHG Emissions | 212.8 | 101.8 |
SCOPE 2 | ||
2.1. Electricity– location-based | 582.7 | 416.4 |
2.1. Electricity– market-based | 302.2 | 414.7 |
2.2. Heat | 5.8 | 15.1 |
2.3. Steam | 0 | 0 |
2.4. Cooling | 0 | 0 |
Total Scope 2 GHG Emissions – location-based | 588.4 | 431.5 |
Total Scope 2 GHG Emissions– market-based | 308.0 | 429.8 |
SCOPE 3 | ||
3.1. Purchased Goods and Services | 1201.3 | 721.8 |
3.3. Fuel and Energy-related Activities | 0 | 0 |
3.4. Upstream Transportation | 3.0 | 3.8 |
3.5. Waste | 25.8 | 14.9 |
3.6. Business Travel | 265.1 | 201.3 |
3.7. Employee Commuting | 58.8 | 56.3 |
3.9. Downstream Transportation | 236.5 | 252.7 |
3.14. Franchises | 0 | 0 |
Total Scope 3 GHG Emissions | 1790.6 | 1250.8 |
Total GHG emissions– location-based | 2591.8 | 1784.1 |
Total GHG emissions– market-based | 2311.3 | 1782.4 |
CO2eq emissions include CH4 emissions. No N2O was emitted during the reporting period.
During the reporting period, biogenic emissions occurred mainly through the production of the supplied electricity in Pisa and Saerbeck and production of the supplied heat (especially at the Bioenergiepark in Saerbeck) and through the treatment of waste. Additional biogenic emissions sources were the use of diesel with a share of biodiesel for company cars (Scope 1) and the use of biodiesel in a rented vehicle for product transportation and business travels, as well as for product (service) deliveries (Scope 3), with a total of 17t of CO2 in 2022 across all these energy and transport sources. Enapter lacked the technical capacity to calculate the amount for 2023.
Non-Methane Volatile Organic Compounds (NMVOC) emissions occurred in the reporting period through the use of chemical compounds in R&D and production, and to a lesser extent through personal and product transportation (commuting and deliveries). NMVOC emissions totalled 2.1 t CO2eq in 2022. Data was not available for 2023.
Enapter’s GHG intensity is provided both including Scope 1, 2, and 3 emissions, as required by ESRS E1-6, paragraph 54, and solely including Scope 1 and 2 emissions – which we believe enables a better comparability of the absolute GHG intensity among companies, since the extent of Scope 3 emissions disclosed can vary widely from one company to another. Furthermore, Enapter believes that the variation of the GHG intensity including only Scope 1 and 2 emissions better reflects a company’s emission reduction efforts, whereas the inclusion of Scope 3 emissions reflects more the evolution of a company’s environment (e.g. decarbonisation of its Tier 2+ suppliers).
The Scope 3 categories 3.2, 3.8, and 3.10 to 3.15 are not yet covered in this report due to a lack of internal capacities to estimate them properly. Enapter aims to expand the Scope 3 estimations to all 15 categories as soon as technically feasible.
Methodologies and assumptions used
Enapter’s Corporate Carbon Footprint (CCF) was calculated for 2022 in the framework of the “Life Cycle Impact Zero” project with the support of Fraunhofer UMSICHT, in line with the GHG protocol. Enapter researched and aggregated all the necessary data while Fraunhofer UMSICHT estimated the CCF based on emission factors from Sphera (GaBi and ecoinvent) and other scientific sources. For 2023, Enapter built on 2022’s calculations but researched additional emission factors when those could not be disclosed by Fraunhofer UMSICHT due to Sphera’s intellectual property rights (around, in particular, 2.1. Electricity and 3.5. Waste).
1.1. Stationary Combustion: These emissions stem entirely from our Saerbeck site. During the construction phase of the Enapter Campus, temporary heating measures were necessary to bridge the gap until the completion of the district heating line that connects the Campus to the Bionergiepark’s biogas plant (expected for 2025). An oil heater was used between July 2022 and October 2022 to dry the production hall, and later to heat our R&D building from October 2022 until April 2023. We then switched to wooden pellet and electric heaters in autumn 2023.
The used energy quantities were known and emission factors for heating oil and wooden pellet are well researched, hence emissions could be easily calculated.
1.2. Mobile combustion: These emissions stem from a few company cars in Pisa, for which Enapter received gas invoices.
1.3. Process emissions: Enapter does not emit greenhouse gases directly, but solely indirectly via the use of Volatile Organic Compounds (VOCs), which are reported separately (see above).
1.4. Cooling: Only our sites in Pisa and Saint Petersburg use air conditioning. In Pisa, regular maintenance operations enable the measurement of possible refrigerant losses.
2.1. Electricity: Enapter worked with a variety of electricity providers across our sites in 2022 and 2023 and switched to a 100% renewable energy-based electricity provider in Pisa in November 2023. The electricity consumption is fully monitored with meters. Supplier-specific emission factors could be identified for most suppliers in 2023, leading to a larger difference between location-based and market-based emission calculations (i.e. a decrease in market-based emissions). Location-based emission calculations used emission factors from the Association of Issuing Bodies6 and Sphera.
2.2. Heat: Heat is entirely electrified in Pisa and stems from natural gas in all other locations except our office at the Bioenergiepark (biogas) and our Campus in Saerbeck (heating oil, wooden pellet and electricity, see above). We read meters in Berlin. In Saerbeck (Bioenergiepark and in the Hahnstrasse temporary office during construction) and Saint Petersburg, we made assumptions based on the office surface area.
3.1. Purchased goods and services: In the framework of the “Life Cycle Impact Zero” study. Enapter in cooperation with Fraunhofer UMSICHT undertook a Life Cycle Analysis (LCA) of all our products that existed at the time: Electrolyser 4 (EL 4), Dryer, Water Tank, Stack module, and Nexus. The electrolyser’s stack was analysed internally for IP protection reasons. The Flex 120 was not included in the study as it was only introduced after completion of the report. The LCAs included a detailed, cradle-to-gate carbon footprint of every component of every product, aggregated at raw material level, using ecoinvent emission factors. This enabled a precise estimation of the carbon footprint of each of our products. For the Nexus, Enapter was not able to carry out rigorous LCA modelling due to the lack of precise data for a significant amount of materials. Instead, we combined and compared an expert estimation on the one hand, and modelling of the available data on the other. For the Flex 120, a rough carbon footprint estimation was undertaken based on the results from the EL 4 and the Nexus.
As a product manufacturer, we assume that the vast majority of the footprint of our purchases stems from the components we purchase to assemble our products. Therefore, we assumed that other purchases of goods, such as small office or lab equipment, and services were negligible in comparison, so we cut them off. For each year, the carbon footprint of our purchased goods corresponds to the estimated carbon footprint of each product (minus emissions from waste and electricity to avoid double-counting from 2.1 and 3.5.) multiplied by the number of products invoiced in the reporting year. There is naturally a time lag between component purchase, product assembly, invoicing and delivery, but the invoicing date is a meaningful calculation boundary, which will well reflect Enapter’s overall economic growth from one year to another.
3.3. Fuel and energy related activities: Enapter did not conduct any fuel and energy related activities in the reporting period.
3.4. Upstream transportation: All transportation emissions from components and materials purchased for the assembly of our products are already accounted for in the cradle-to-gate carbon footprinting of our products under 3.1. They are hence cut off here to avoid double-counting. The only emissions remaining are from product transportation between our warehouses and factory in Pisa, through a rented minivan, for which we have invoices indicating how many litres of diesel were used.
3.5. Waste: Waste quantities were differentiated by waste types (CER codes), company sites and origin (R&D, Production or Office). R&D and production waste was traced at source (waste containers) and yearly quantities estimated based on an on-site observation of a representative sample. Office waste at all company sites was estimated based on the BSR office waste calculator7 and re-adjusted to be more realistic based on discussions with local office managers. For 2022, Fraunhofer UMSICHT multiplied the waste quantities by emission factors from ecoinvent and their own modelling for the respective handling of waste and added emissions from the transportation of waste to the respective waste management facility. Since these emission factors are protected by ecoinvent’s intellectual property rights, Enapter extensively researched publicly available emission factors for the handling (and transportation) of waste, and calculated the total carbon footprint for 2022 anew, landing on a final result in the same order of magnitude as that calculated by Fraunhofer UMSICHT. We then applied these new emissions factors to calculate the carbon footprint for 2023, and will keep doing so in the future, which makes estimations comparable between years.
3.6. Business travels: Data pertaining to our business travels was gathered via Enapter’s internal travel expense accounting systems and supplemented where needed with a search of individual calendars and/or requests to individual colleagues. The following transportation means are taken into account: combustion car, electric car, train, short-haul flight, long-haul flight and long-haul flight business class. Distances are estimated with google maps for car and train travels, and with www.airmilescalculator.com and https://klima-kollekte.de for flights. They are multiplied by emission factors from Allekotte8 and atmosfair gGmbH.9 Taxi and public transport rides were deemed negligible and cut off. Emissions from overnight stays in hotels are deliberately left out, because the data gathering effort for this category is deemed too high compared to the expected insights and action levers: overnight stay emissions should be roughly proportional to business travel emissions, with little to no reduction potential beyond mere business travel reductions.
3.7. Employee commuting: Enapter conducted a company-wide online commuting survey to determine as precisely as possible the employees’ commuting distances, frequencies and transportation means. The survey was made compulsory for all employees in 2022 (with a response rate of 100% in June 2023), and voluntary in 2023 (with a response rate of 51% in January 2024). Where employees did not answer the survey or had left the company, extrapolation rates were factored in (with a differentiation by company site) to make up for missing answers. The commuting survey took the following transportation means into account: combustion car, electric car, public transportation, bicycle or walking. The total distance for each transportation means is multiplied by emission factors from Allekotte.10
3.9. Downstream transportation: Since Enapter delivers predominantly “Ex Works”, product shipments are mainly the responsibility of our clients. We retrieve all shipment information (product types and shipping addresses) from Enapter’s internal bookkeeping system. from which we derive the product gross weight, and the transportation means and distance. All deliveries within continental Europe are assumed to be by truck, and all other deliveries are assumed to be by airfreight. Distances are estimated with google maps for truck shipments and with https://klima-kollekte.de for airfreights. Only full product shipments (e.g. electrolysers, dryers) are accounted for; spare part deliveries are deemed negligible and cut off.
3.14. Franchises: Enapter did not operate franchises in the reporting year.
DR E1-7: GHG Removals and GHG mitigation projects financed through carbon credits
Before considering funding GHG removal and mitigation projects. Enapter is prioritising the strong reduction of its own Scope 1 and 2 emissions as advised by experts (e.g. SBTi). Nonetheless, we have undertaken a thorough analysis of carbon compensation opportunities and had in-depth exchanges with many key experts and project implementers, but we remain concerned about the current debate on the credibility of compensation projects.11 For this reason, we have decided to hold our decision for at least another year, hoping not only to reduce our emissions further, but also counting on the carbon offsetting sector to provide more clarity on the effectiveness of their projects until then.
ESRS E2 Pollution
DR related to ESRS IRO-1 – Description of the processes to identify and assess material pollution-related impacts, risks and opportunities
Enapter possesses two R&D and production sites in Pisa and Saerbeck that could potentially entail pollution risks to air, water and soil. Each site has its own Health & Safety Manager, who is responsible for continuously monitoring and evaluating pollution risks among others. They closely trace all of Enapter’s resource inflows and outflows and ensure the safety of our employees and the integrity of the environment in all processes. They perform regular site inspections, ask relevant colleagues about their daily practices and potential problems they encounter and solve them if necessary.
DR E2-1: Policies related to pollution
Enapter’s Environmental Policy is published on our company’s website and covers pollution in paragraphs 3 and 4.12
DR E2-2: Actions and resources related to pollution
Enapter Srl in Italy is currently applying for the Single Environmental Authorization (Autorizzazione Unica Ambientale – AUA). The Single Environmental Authorisation is a legal requirement, in accordance with Legislative Decree 152/2006, which lays down rules on environmental protection and waste management. The standard applies to the protection of air, water and soil by industries and production activities in general. The decree does not apply to R&D activities, which is why Enapter Srl has not been subject to authorisation to date.
We are also aiming at the Environmental Management System Certification (ISO 14001) in the future for our Pisa and Saerbeck sites, and already starting to develop corresponding monitoring systems, among others for the prevention of pollution.
Following a crack in an air conditioner at our Pisa plant, which led to a leak of 33 litres of refrigerant R410A in December 2023, Enapter inspected all air conditioners in Pisa and is currently advising on measures to improve the maintenance and to reduce the risks and consequences of leaks, for example by making controls more frequent and thorough, and/or by switching to a less emitting type of refrigerant.
We are improving certain production processes with a view to reducing water consumption. and we recover wastewater from production for filtration and treatment before its content is re-used or recycled.
DR E2-4: Pollution of air, water and soil
Enapter emits VOCs (Volatile Organic Compounds) in quantities not subject to environmental authorisation and mainly for R&D activities. The new chemical plant being installed in Pisa at the time of reporting is expected to emit some dust, for which there will be an activated carbon filter system with a triboelectric sensor that measures the presence of dust in the air stream. Dust abatement through filters reduces the presence of pollutants that may escape the control system to a non-significant threshold. In case of system malfunction, the chemical plant is automatically turned off. For the protection of water, all production effluents are not fed into the sewerage system but treated as waste. Enapter does not emit anything into the soil and does not emit any pollutants into the air, water and soil exceeding the thresholds listed in Annex II of Regulation (EC) No 166/2006 of the European Parliament and of the Council (European Pollutant Release and Transfer Register “E-PRTR Regulation”).
The water used to clean the chemical equipment is disposed of as waste, although this waste is non-hazardous. However, in order to reduce the environmental impact. Enapter prefers such water to be handled by companies specialising in water treatment and recovery. Contaminated solids, such as disposable gloves, paper towels, etc., are collected in separate containers and disposed of as special waste by specialised waste treatment partners.
Beyond its own R&D and production facilities, Enapter faces an indirect pollution risk via the global distribution of its AEM electrolysers, mainly in two ways. First, the electrolysers contain a very basic KOH solution, which needs to be replaced by users once a year. KOH needs proper treatment (addition of acid to neutralise its pH) before it can be released without concern in the environment. Second, the electrolyser’s stack, which is a hermetically closed system, contains various hazardous substances, which need to be disposed of properly at the end of life of the electrolysers. In order to avoid improper disposal of the stacks and potential environmental pollution, Enapter’s clients are required by contract to send us back their electrolysers. Read more about our circularity and reverse logistics approach below, under ESRS E5.
Enapter does not emit microplastics. Beyond the above-mentioned refrigerant leak, Enapter did not register any significant pollution to air, water and soil during the reporting period.
DR E2-5: Substances of concern and substances of very high concern
Enapter does not produce, distribute, commercialise or import/export any substances of concern and substances of very high concern, on their own or in mixtures. We use some of these substances in small quantities (<250g / year) for R&D purposes.
ESRS E5 Resource Use and circular economy
DR E5-1: Policies related to resource use and circular economy
Enapter’s Environmental Policy covers resource use in its paragraph 3, and circular economy in its paragraph 12.13
DR E5-2: Actions and resources related to resource use and circular economy
Enapter is already asking all EL customers to send their electrolysers back at their end of life. In 2022, Enapter developed a reverse logistics process, defining how to recover and disassemble returned products, and how to evaluate and sort components for re-use, repair or recycling. Furthermore, we have also defined an evaluation process for 25% of the components of returned electrolysers already. We plan to finalise this process in 2024 and to implement recycling step by step, starting with the most obvious, highly valuable and recyclable components.
Enapter progressively started commercial distribution in 2017. We anticipate to only receive significant amounts of end-of-life products after 2032. This leaves us ample time to prepare and implement all necessary administrative, technical and logistical steps to set up a circular manufacturing system. Enapter strives to optimise its water usage, especially at its R&D and production site in Pisa. While tracing which activities use the most water, we identified the de-ionisation of tap water (needed for R&D and testing purposes) as a highly water-consuming process. Therefore, we are currently looking at ways to re-use wastewater from water distillation as grey water, for example for toilets or laboratory hygiene.
DR E5-3: Targets related to resource use and circular economy
Enapter plans to grow strongly in the foreseeable future as the green hydrogen industry progressively replaces part of the fossil fuel industry. This means that the amount of new products we put on the market will surpass the amount we recover and refurbish for a long time. This said, taking into consideration our product design, our growth rate, our product lifespan and our re-using capacities, we believe that we should be able to re-use approximately 10% (in weight) of our product components by 2030, and 45% by 2050. Where product components cannot be re-used, we should be able to recycle approximately 40% of them14 (in weight) as we start recovering products, and we expect recycling capacities to increase progressively as the recycling market matures. We will also support this market by requesting recycled materials from our suppliers wherever possible.
DR E5-4: Resource inflows
As a product manufacturer, the largest part of our resource inflow stems from the raw materials and components we purchase to produce and assemble our products. A general description of the material composition of our electrolysers can be found below under DR E5-5: Resource outflows. Similar raw materials and components are purchased for R&D purposes, in particular chemical compounds such as solvents. Beyond these regular inflows, Enapter also occasionally invests, for example, into new R&D, Production and/or office equipment. Additionally, in 2022, Enapter built its new R&D and production site in Saerbeck, including a production hall and an R&D building. Due to the sheer complexity of these investment inflows and the lack of a methodology to properly depict them, the table below focuses on summing up the regular inflows.
Resource Inflows | 2023 | 2022 |
Total weight of products and technical and biological materials used (t)15 | 214.40 | 149.93 |
Percentage of biological materials (and biofuels used for non-energy purposes) used to manufacture the undertaking’s products and services (including packaging) that is sustainably sourced | 64% | 64% |
Water (m³) | 5.299 | 3.815 |
The total weight of products used was calculated based on the known gross weight and total invoiced numbers of products for a given year. No biological material is used for our products. except for the packaging of the purchased components (inbound packaging) and the packaging of the delivered products (outbound packaging) – in both cases cardboard boxes. The percentage of sustainably sourced cardboard boxes (specifically: FSC-certified) was estimated based on observation of a representative sample for inbound packaging and is known from the supplier for outbound packaging. Inbound and outbound wooden pallets were cut off from the calculation due to a lack of traceability at this stage. They are assumed to be widely re-used.
The total water consumption was calculated based on water bills, except for the office in Hahnstrasse, Saerbeck, and the Saint Petersburg office, where they were estimated based on office surface area and occupancy rate.
DR E5-5: Resource outflows
Circular product design
As a product manufacturer, the most impactful measure we can take to preserve the environment is to reduce our demand for natural resources to a minimum. We are fully aware that we need to handle natural resources carefully because raw materials are precious, and waste is becoming an increasing challenge around the globe. This is why we are planning to circularise our production as much as possible.
In this endeavour, we have already developed a reverse logistics process and a recycling evaluation process (see DR E5-2, p. 24).
Our electrolysers, dryers and water tanks are designed for disassembly, with most of their components being assembled with screws (as opposed to being glued or soldered). Most metallic, plastic and electronic parts have a very long lifespan and can potentially be re-used at the end of life of the products. When customers send back faulty products under warranty, they are always refurbished and sent back to them. Repairs take place by identifying and repairing or replacing the component(s) causing the issue.
Products and materials
The core of our technology is the iridium-free AEM stack, which can be mounted into a single-core electrolyser or at any scale into multi-core systems (e.g. Flex 120, Nexus 500 or Nexus 1000). Our single- and multicore electrolysers are composed of around two-thirds of metals (i.e. steel, aluminium, nickel), around 20% of plastics, around 10% of electronics, and around 2% of chemical compounds. The single-core electrolysers are packed in a cardboard box, padded with plastic foam and mounted on a wooden pallet. Approximately 75% of the materials used are recyclable (93% of the packaging), and an additional 6% are recyclable after component disassembly.
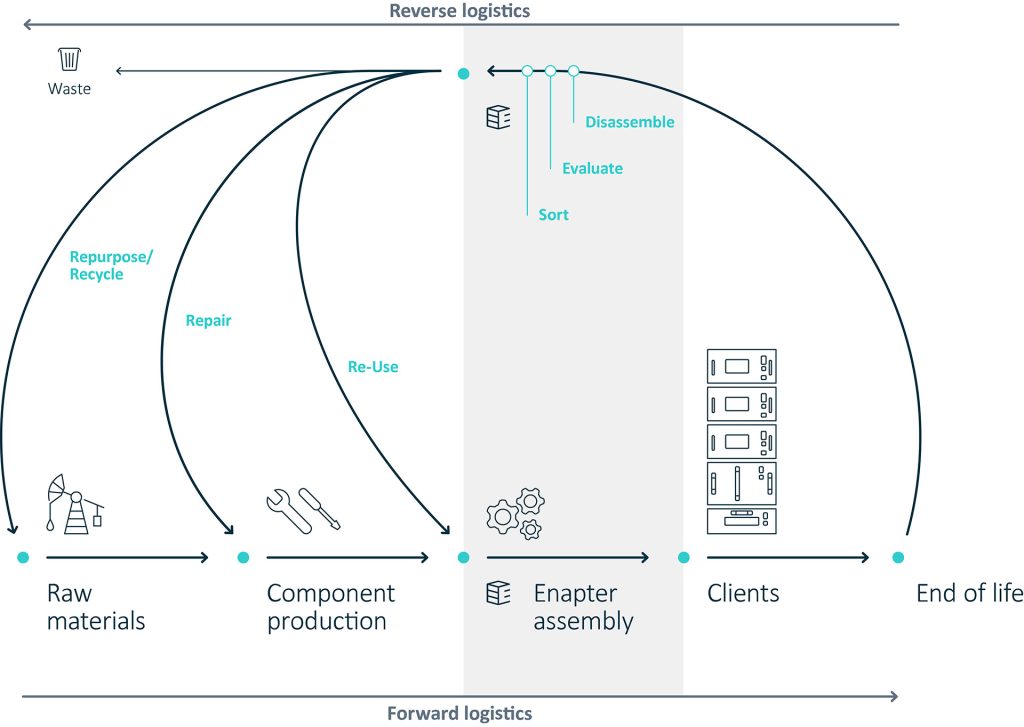
Waste reduction and waste management strategy
Waste is dealt with in Article 3 of Enapter’s Environmental Policy16 Enapter implements this policy incrementally, including currently in the following concrete ways:
- Continuous improvement of the waste inventory and tracking system
- New product design with a view to reduce chemical production waste
- On-going discussions with new recycling partners, in order to increase Enapter’s recycling rate
Additional measurement of emissions to air
Resource Outflows – Waste | 2023 | 2022 | ||
Total amount of waste generated (t) | 142 | 87 | ||
Waste intensity (t / M€ revenues) | 4.50 | 5.90 | ||
Hazardous waste | Non-hazardous waste | Hazardous waste | Non-hazardous waste | |
Total amount by weight diverted from disposal (t): | 2.08 | 124.06 | 0.00 | 75.63 |
Re-use | 2.08 | 19.73 | 0.00 | 0.00 |
Recycling | 0.00 | 104.32 | 0.00 | 62.01 |
Other | 0.00 | 0.00 | 0.00 | 13.62 |
Total amount by weight directed to disposal (t): | 6.49 | 9.00 | 0.69 | 10.28 |
Incineration | 2.34 | 8.68 | 0.55 | 8.58 |
Landfill | 0.00 | 0.33 | 0.00 | 1.70 |
Other | 4.16 | 0.00 | 0.14 | 0.00 |
As a manufacturer of electrolysers, our main waste streams are composed of cardboard, metals (in particular, stainless steel, aluminium and nickel), electronics (in particular, populated printed circuit boards), chemical compounds (in particular, halogenated solvents and other solvents), and typical office waste (paper, plastics, metals, organic, glass, residual). Enapter does not generate any radioactive waste.
Enapter’s calculation methodology to track and report waste is based on three main sources:
- Direct measurement
- Secondary data derived from the expert knowledge of colleagues
- Secondary data derived from scientific or other sources
Whenever possible, these different sources are cross-checked against each other for consistency.
For example, the amount of cardboard waste in Pisa (around 35 tons in 2022, Enapter’s single largest waste type by weight) was estimated based on:
- Direct observation of the local paper containers
- Knowledge of yearly amount of containers picked up
- Weight/volume conversion factor from a secondary source (Statistisches Landesamt Bayern) matching our direct observation
- Comparison of the order of magnitude of this estimation with another estimation based on total purchase volume and gross weight, and estimated proportion of packaging weight.
Social Information
ESRS S1 Own workforce
Please refer to the corresponding disclosures on page 8.
DR S1-1: Policies related to own workforce
Enapter perceives its own workforce as one of its most valuable resources. We are convinced that maintaining a well-trained, highly motivated and productive workforce is key to our business success. Optimal working conditions build employee loyalty and keep them motivated and productive. These include secure employment contracts, adequate and flexible working hours, a healthy work-life balance, a safe working environment, competitive wages, and career development opportunities. Moreover, the clear commitment to treat everybody equally irrespective of their gender, religion, origin, sexual orientation or disability is another strong factor of motivation and productivity. At Enapter, wages are based on work experience, level of responsibilities and a regular market benchmarking. Our health and safety officers in Italy and Germany ensure safe working conditions to all and provide regular safety trainings, which led to having only one minor incident happen during the reporting period. Harassment in the workplace is explicitly prohibited by Enapter’s Code of Conduct and can be reported by employees via the Whistleblower mechanism. We welcome diversity and counted no less than 22 nationalities among our employees as of 2023.
Enapter has adopted a Human Resources Policy, which sets a framework for how our company deals with its own workforce and workers in our supply chain. The policy can be found on Enapter’s website.
DR S1-6: Characteristics of the Undertaking’s Employees
Own Workforce | Disclosure Requirements | 2023 | 2022 |
S1-6 – Characteristics of the undertaking’s employees | Head count of the total number of employees (as of 31st Dec 2023) | 215 | 250 |
…and breakdown by gender | 70 female 145 male | 75 female 175 male | |
Number of permanent employees | 191 | 241 | |
…and breakdown by gender | 57 female 132 male | 72 female 169 male | |
Number of temporary employees | 22 | 9 | |
…and breakdown by gender | 13 female 9 male | 3 female 6 male | |
Number of non-guaranteed hours employees | 2 | 0 | |
…and breakdown by gender | 2 male | N/A | |
Number of employees who have left the undertaking during the reporting period | 100 | 26 | |
Employee turnover rate | 27,66% | 11,50% |
DR S1-7: Characteristics of non-employee workers in the undertaking’s own workforce
Own Workforce | Disclosure Requirements | 2023 | 2022 |
S1-7 – Characteristics of non-employees in the own workforce | Total number of non-employees in the own workforce, i.e., either people with contracts with Enapter to supply labour (“self-employed people”) or people provided by undertakings primarily engaged in “employment activities” | 4 | GmbH: unknown Other entities: 0 |
DR S1-8: Collective bargaining coverage and social dialogue
Own Workforce | Disclosure Requirements | 2023 | 2022 |
S1-8 – Collective bargaining coverage and social dialogue | Percentage of total employees covered by collective bargaining agreements | 64.65% | 54.80% |
Existence of one or more collective bargaining agreements | 1 | 1 | |
Global percentage of employees covered by workers’ representatives | 6.05% | 5.52% |
DR S1-9: Diversity metrics
Own Workforce | Disclosure Requirements | 2023 | 2022 |
S1-9 – Diversity indicators | Gender distribution at top management (number) | 1 out of 7 | 0 out of 4 |
Gender distribution at top management (percentage) | 14,29% | 0,00% | |
Number of employees by age group: <30 years old… | 69 | 99 | |
… between 30 and 50 years old… | 128 | 132 | |
… and >50 years old | 18 | 17 |
DR S1-10: Adequate Wages
Own Workforce | Disclosure Requirements | 2023 | 2022 |
S1-10 Adequate wage | Percentage of employees paid an adequate wage | 100% | 100% |
Percentage of non-employees paid an adequate wage | 100% | GmbH: 100% Others: N/A |
DR S1-11: Social protection
Own Workforce | Disclosure Requirements | 2023 | 2022 |
S1-11 – Social protection | Percentage of employees covered by social protection in case of sickness, unemployment, employment injury and acquired disability, maternity leave, retirement | 100% | 100% |
DR S1-12: Persons with disabilities
Own Workforce | Disclosure Requirements | 2023 | 2022 |
S1-12– Persons with disabilities | Percentage of persons with disabilities… | 3% | 2% |
…broken down by gender | 33% female 66% male | 33% female 66% male |
DR S1-13: Training and Skills Development metrics
Own Workforce | Disclosure Requirements | 2023 | 2022 |
S1-13 – Training and skills development indicators | Percentage of employees that participated in regular performance and career development reviews… | SRL and GmbH: unknown LLC and AG: 0 | SRL and GmbH: unknown LLC: 0 |
…broken down by gender | See above | See above | |
Average number of training hours per person for employees… | SRL: 5.86 GmbH: unknown LLC and AG: 0 | SRL: 15h GmbH: unknown LLC and AG: 0 | |
…broken down by gender | SRL and GmbH: unknown LLC and AG: 0 | SRL and GmbH: unknown LLC and AG: N/A |
DR S1-14: Health and safety metrics
Own Workforce | Disclosure Requirements | 2023 | 2022 |
S1-14 – Health and safety indicators | Percentage of own workers covered by its health and safety management system | 100% | 100% |
Number of fatalities as a result of work-related injuries and work-related ill health | 0 | 0 | |
Number of recordable work-related accidents | 0 | 2 | |
Rate of recordable work-related accidents | 0 | 0.008 | |
Number of cases of recordable work-related ill health | 0 | 0 | |
Number of days lost to work-related injuries and fatalities from… work-related accidents | 0 | 7.5 | |
… work-related ill health | 0 | 0 | |
… and fatalities from ill health | 0 | 0 | |
Number of fatalities of other workers working on the undertaking’s sites. | 0 | 0 | |
Percentage of own workers covered by a legal and/or standardised and audited health and safety management system | 100% | 100% |
DR S1-15: Work-life balance
Own Workforce | Disclosure Requirements | 2023 | 2022 |
S1-15 – Work-life balance indicators | Percentage of employees entitled to take family-related leaves | 100% | 100% |
Percentage of entitled employees that took family-related leaves… | 22% | 11% | |
… and a breakdown by gender | 24 female 23 male | 12 female 16 male |
DR S1-16: Remuneration metrics (pay gap and total remuneration)
Own Workforce | Disclosure Requirements | 2023 | 2022 |
S1-16 – Compensation indicators (pay gap and total compensation) | Male-female pay gap | 20,93% | 21,04% |
Ratio of the annual total compensation ratio of the highest paid individual to the median annual total compensation for all employees | 3,81 | 3,02 |
DR S1-17: Incidents. complaints and severe human rights impacts
Own Workforce | Disclosure Requirements | 2023 | 2022 |
S1-17 – Incidents, complaints and severe human rights impacts and incident | Total number of incidents of discrimination, including harassment, and any related material fines, sanctions or compensation | 0 | 0 |
Governance Information
ESRS G1 Business conduct
DR related to ESRS 2 IRO-1 – Description of the processes to identify and assess material impacts. risks and opportunities
Please refer to Disclosure Requirement IRO 1: Description of the processes to identify and assess material impacts, risks and opportunities, p.11.
DR G1-1: Business conduct policies and corporate culture
Enapter has adopted a Code of Conduct, which has been distributed via email to all employees in April 2023 and published on Enapter AG’s website17. The Code of Conduct covers all topics relevant to the good conduct of business, including, but not limited to, human rights across our supply chain, health and safety, compliance, prohibition of bribery and corruption, and a whistleblower mechanism. This Code of Conduct is also an integral part of the Employee Handbook, which is distributed systematically to all new workers upon recruitment.
In particular, the whistleblower mechanism enables both Enapter employees and external stakeholders to report any violations or substantiated suspicions of violations of legal provisions, especially criminal offences, administrative offences or significant violations in connection with the business operations of the Enapter Group, to an external law firm who established a reporting office to this end. The report can be submitted by all means of communications (email, mail, phone) and the mechanism ensures absolute confidentiality, anonymity and the absence of reprimands.
The Code of Conduct’s provisions on the prohibition of corruption and bribery are consistent with the goals of the United Nations Convention against Corruption.
DR G1-2: Management of relationships with suppliers
Enapter’s overall resilience, performance and success are highly dependent on its supply chain. We aim to establish long-term relationships based on trust with our suppliers. Therefore, we foster a collaborative and responsive communication culture with our suppliers, striving to address their requests as soon as they occur.
We select our suppliers in a fair manner based on objective criteria, in particular quality, reliability, cost, and social and environmental practices. We review and update these criteria to align with evolving business goals and market conditions. Our Supply Chain Management, Quality and Logistics Departments consolidate rating methods jointly and use vendor ratings and score cards to structure the evaluation of our suppliers. A supplier questionnaire helps with the collection of all the necessary information about their practices. Enapter plans to gradually centralise the data collection and automate the questionnaires to avoid risks of negative human interferences in the evaluation process. As of March 2024, we have secured the approval of our Code of Conduct by 55 of our largest suppliers and requested approval from another 55 of them. We plan to extend this request to several hundred more suppliers in the course of 2024. In the reporting period, we paid a visit to 25 suppliers and carried out two audits via our Supplier Quality Engineer. Social and environmental responsibility clauses are already included in our supplier contracts.
Enapter pays particular attention to the needs of SMEs among our suppliers, and while we align with the payment terms of all our suppliers, we willingly prioritize payments to SMEs.
DR G1-3: Prevention and detection of corruption and bribery
Enapter’s Code of Conduct (Article 9) specifically prohibits corruption and bribery. The Code of Conduct is an integral part of the Employee Handbook. which is distributed systematically and bindingly to all new workers upon recruitment. A whistleblower mechanism enables the prevention and detection of potential instances of corruption and bribery. Employees and external stakeholders have the possibility to report suspicions or proven cases anonymously to an external law firm, which, after evaluation, reports to the Enapter AG. Internal trainings on corruption prevention, and Enapter’s Code of Conduct and whistleblower mechanism will be organised on a regular basis.
DR G1-4: Confirmed incidents of corruption or bribery
2023 | 2022 | ||
G1-4 – Confirmed incidents of corruption or bribery | Total number and nature of confirmed incidents of corruption or bribery | 0 | 0 |
Number of convictions and the amount of fines for violation of anti-corruption and anti-bribery law | 0 | 0 | |
Number of confirmed incidents in which own workers were dismissed or disciplined for corruption or bribery-related incidents | 0 | 0 | |
Number of confirmed incidents relating to contracts with business partners that were terminated or not renewed due to violations related to corruption or bribery | 0 | 0 |
DR G1-5: Political influence and lobbying activities
Enapter does not support, either financially or in-kind, any political parties, their elected representatives or persons seeking political office, in any country. None of Enapter’s Advisory Board members is an elected politician or candidate for office.
Enapter is a paying member of the following German (trade) associations:
- Landesverband Erneuerbare Energien NRW (as a Board member)
- Erneuerbare Energien Hamburg Clusteragentur (EEHH)
- Bundesverband Energiespeicher Systeme (BVES)
- Energieland2050 e.V. of the Steinfurt district
and a non-paying member of the following European organisations:
- Renewable Hydrogen Coalition
- Cleantech Scale-Up Coalition
Enapter’s Managing Director for the GmbH Philip Hainbach is in charge of Public Affairs, among other matters. As such, he represents Enapter within the aforementioned associations and generally coordinates Enapter’s relationships with political decision-makers. Enapter’s VP Strategy and Business Development Tim Cholibois also represents Enapter at various events, including discussion panels where he occasionally meet political decision-makers. All are committed to the success of the scale up of the hydrogen industry at national, European and international level.
DR G1-6: Payment practices
As a payer, Enapter is not in a position to set its own standard payment terms, but aligns with those of the suppliers, which are generally 30 days from the invoice date. In practice, Enapter has also been paying, on average, around 30 days after the invoice date during the reporting period and always prioritising payment to smaller companies if needed. There were no legal proceedings for late payments during the reporting period.
Footnotes
- The SBTi (https://sciencebasedtargets.org) recommends company to decrease their 2020 emissions by 42% until 2030. ↩︎
- https://www.clean-hydrogen.europa.eu/knowledge-management/strategy-map-and-key-performance-indicators/clean-hydrogen-ju-sria-key-performance-indicators-kpis_en ↩︎
- Estimation based on an emission factor of 0,0003144 tCO2eq / kWh for the Italian electricity grid (Association of Issuing Bodies 2023). ↩︎
- Enapter AG Consolidated Financial Statements as of Dec. 31, 2022, p.19 Source: https://www.enapterag.de/wp-content/uploads/2023/04/Annual-Report-Enapter-2022.pdf ↩︎
- Enapter AG Consolidated Financial Statements as of Dec. 31, 2023, p.21 Source: https://enapterag.de/wp-content/uploads/2024/04/Enapter-Konzernabschluss-2023-en.pdf ↩︎
- https://www.aib-net.org/facts/european-residual-mix ↩︎
- https://www.bsr.de/abfallrechner-23203.php ↩︎
- https://www.umweltbundesamt.de/sites/default/files/medien/1410/publikationen/2020-06-29_texte_116-2020_tremod_2019_0.pdf ↩︎
- https://www.atmosfair.de/wp-content/uploads/atmosfair-methode-flugberechnung-21112022.pdf ↩︎
- https://www.umweltbundesamt.de/sites/default/files/medien/1410/publikationen/2020-06-29_texte_116-2020_tremod_2019_0.pdf ↩︎
- Criticism about the effectiveness of carbon offsetting projects arose particularly after the following article from The Guardian: Revealed: more than 90% of rainforest carbon offsets by biggest certifier are worthless, analysis shows | Carbon offsetting | The Guardian ↩︎
- We minimise waste production, track our waste across our supply chain, constantly improve our recycling rate, avoid emissions to air, soil and water, and dispose of our waste in compliance with local legislation. 4. We pay particular attention to how we handle hazardous substances and ensure the safe management of chemicals, in line with all applicable regulations, in order to protect the health of our employees, as well as public health and the environment at large. We aim to minimize the use of hazardous substances and prioritize the use of environmentally friendly materials in our manufacturing processes. ↩︎
- We minimise waste production [and] constantly improve our recycling rate. 12. In line with circular economy principles, we plan to set up a disassembly line to re-use, repair and recycle as many of our product components as possible at their end of life, thereby minimising our reliance on natural resources. ↩︎
- These estimations stem from Enapter’s Transition plan for climate change mitigation, an internal reflection and planning tool aiming at paving our way towards zero GHG emissions and environmental impact by 2050. The plan shows how the evolution of our industrial production, revenues, human resources, and product design can positively impact our Corporate Carbon and Environmental Footprint. ↩︎
- These numbers are based on an estimation of the total weight of products invoiced in the reporting year, including inbound and outbound packaging. Due to the possible time lag between invoicing and payment, they might not reflect the company’s growth as depicted in the financial report. ↩︎
- We minimise waste production, track our waste across our supply chain, constantly improve our recycling rate, avoid emissions to air, soil and water, and dispose of our waste in compliance with local legislation. ↩︎
- https://enapterag.de/en/code-of-conduct/ ↩︎